点击上方↑模具工业,关注我们吧
《模具工业》新的投稿系统正式上线啦!点击(模具工业 (cnki.net))在线办公系统中的作者投稿系统,注册后按提示操作就可投稿,欢迎投稿!
1 冲铆工艺有限元建模
1.1 冲铆几何模型建立
1.2 材料设置
表1 模型参数设置

表2 材料参数
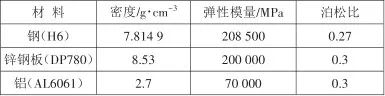
1.3 接触和边界条件设置
1.4 网格划分
(a)上板网格划分 (b)下板网格划分 (c)总体网格划分
2 正交试验方案设计
2.1 试验方案
表3 变量参数试验水平表 ( mm )
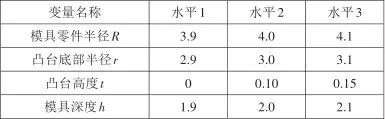
2.2 试验结果
图5 冲铆成形后截面几何形状
表4 正交试验结果 ( mm )
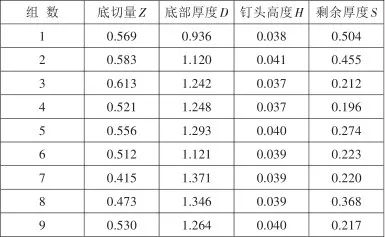
3 铆模参数对接头截面成形质量影响分析
3.1 底切量结果分析
表5 截面底切量极差分析
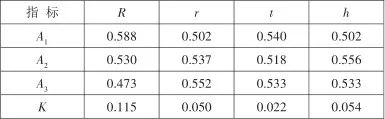
3.2 底部厚度结果分析
表6 截面底部厚度极差分析
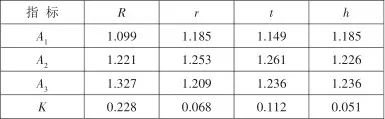
3.3 钉头高度结果分析
表7 截面钉头高度极差分析
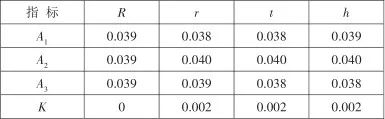
3.4 剩余厚度结果分析
表8 截面剩余厚度极差分析
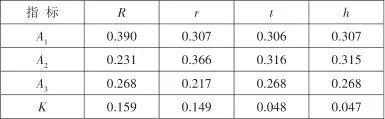