来源:《锻造与冲压》2023年24期
刘鹏, 茹承曦, 尤宝卿, 聂飞, 徐冬生, 柯亮 · 东实(武汉)实业有限公司
“中国制造2025”行动纲领的提出对车用金属轻量化材料提出了比以往更高的要求,车体轻量化和材料生产及尾气排放的节能环保,是新时期车用材料生产工艺大势所趋。
热冲压成形技术利用了材料高温状态下良好的成形性,可有效减少回弹,又能保证模具寿命,而成形淬火后的构件具有超高强度,同时价格合理,因此热冲压成形技术是实现汽车轻量化和安全性的先进成形技术。热冲压成形技术已得到世界各国钢铁和汽车制造厂商的高度重视和广泛应用。据不完全统计,截至2018 年,全世界已至少共有400 条以上的热冲压生产线,而中国已有130 多条热冲压生产线和试模生产线。目前应用较广泛的热成形用钢为22MnB5。随着热成形钢应用越来越广泛,涉及到的产品类型也越来越多,也就给各种零件的热成形工艺开发带来了新的挑战。
零件与材料
踏板横梁零件
本文分析对象为某合资品牌小型乘用车平台化车身用踏板横梁零件,如图1 所示。踏板横梁位于车身中部,连接前地板,中通道,后端;两侧与门槛连接板搭接,四周均存在焊接焊点,因此对零件精度尤其是Y 向宽度要求极高。
图1 踏板横梁
材料性能
该零件所选用材料为22MnB5 AS23/23,实际定义材料牌号为NSSQAS1500H AS23/23,料厚(1.0±0.055)mm;初始态的22MnB5 材料微观组织为铁素体/珠光体,抗拉强度350MPa ~600MPa,均匀延伸率约为15%。通过热冲压成形技术在模具内冷却淬火后得到完全的马氏体组织,抗拉强度可达到1500MPa,均匀延伸率约为6%。其化学组成如表1 所示。
表1 NSSQAS1500H AS23/23 化学成分
注:Ceq=C+(Mn+Si)/6
热成形工艺
超高强度钢板热冲压工艺是将超高强度钢板加热到奥氏体化温度以上,适当保温后,快速移动到带有冷却系统的模具上并快速冲压,成形的同时进行淬火冷却,最后获得超高强度热冲压件的一种成形工艺,其过程如图2 所示,通过该工艺可以将零件的抗拉强度提升至1500MPa 以上。
图2 热成形过程
基于Autoform 的数值仿真
成形分析
⑴冲压方向。
由于该踏板横梁零件两侧存在沿车身X 向和Z向的翻边面,如图3 所示;为实现该翻边造型,同时考虑到冲压前板料托料状态,最终确定冲压方向如图4 所示。
图3 X/Z 向翻边
图4 冲压方向
⑵成形顺序及工艺补充面。
确定冲压方向后,零件截面呈斜“N”形,其成形顺序为:先成形出主斜面1,再成形两侧斜面2,最后完成翻边面3 成形,如图5 所示。
图5 成形顺序
根据冲压方向、成形顺序,完成工艺补充面的设计,将该工艺面导入Autoform 并进行网格划分,如图6 所示。
图6 工艺面和有限元网格划分
有限元分析路径
热成形零件成形所需的工艺路径为:加热至930~950℃并保温完成奥氏体化→将板料快速转移至模具内→压机下行完成冲压→保压。在仿真分析模拟中各参数需与现场实际工业化过程保持一致,以获得最真实的模拟结果。
模型建立
本文基于Autoform 软件建立踏板横梁热冲压成形分析的有限元模型,如图7 所示。工具体由凸模,凸模压边圈,凹模,凹模压边圈组成。板料初始温度为930℃,工具体初始温度为75℃。
图7 工具体设置
成形性评价
⑴减薄率。
热冲压时,伴随着应变的过程,如果各部分材料越能够均匀地承担成形所需的材料流动,那么板料的各部分应变就会越小,其减薄率也会越小,也就越不容易发生破裂现象。在相同的工艺参数下,最大应变越小,那么就可以说其热成形性越好。经多次仿真模拟得到减薄分布图如图8 所示,对于该踏板横梁,在热冲压时最大减薄值出现在零件的凸筋区域,即开裂风险点就在凸筋圆角处,只要保证该区域的减薄值在一定范围内就不会发生破裂的缺陷。
图8 减薄分布图
图9 板料冲压成形过程
⑵成形过程。
在热冲压过程中,材料流动过程决定了零件是否会出现起皱或叠料现象。因板料在加热后,塑性增强,变形阻力变小,在未发生叠料前的波浪往往会被压平而形成局部增厚,如果材料流动过快就易形成叠料,因此需要关注成形过程,避免出现叠料情况。
参数对热成形过程的影响
⑴拉延筋。
拉延筋是指在压料面上设置的凸起形状,热成形中主要采用圆形拉延筋。在热成形工艺中拉延筋的主要作用表现在以下几个方面:
①控制进料阻力。适当配置拉延筋各项参数,增加板料变形区的进料阻力。
②调节进料阻力的分布。可提高坯料流动的稳定性,得到均匀变形的冲压件。
③避免出现内皱。可防止因凸缘周边材料不均匀流动产生的皱纹进入修边线内,减轻或消除复杂零件悬空部分因材料集中而发生的内皱现象。
⑵压边间隙。
在热成形工艺中,拉延筋的载体通常为压边圈,拉延筋和压边间隙配合形成稳定的流料阻力。随着压边间隙的逐渐减小,流料阻力增加,零件减薄率随之增加甚至出现开裂;如压边间隙过大,拉延筋和压边圈无法对板料形成约束,易形成起皱甚至叠料。
⑶成形速率。
针对应变速率对冲压件减薄的影响所做的研究结果显示,冲压件的厚度减薄率随应变速率的增大而减小。不同温度下减薄率随应变速率的变化有明显差异:温度低于500℃时,变化趋势较小;温度高于500℃时,减薄率的减小趋势明显,如图10 所示。
图10 不同温度下最大减薄率随应变速率的变化
⑷成形温度。
板料自加热炉转运至模具内的时间决定了板料成形的温度,热成形零件完全淬透的温度通常在700℃以上。对比图11 中的四组曲线可知,同一成形温度下,冲压件中性层的最大主应变随着应变速率的增大而逐渐减小。且温度越高时,主应变的应变值越大,即温度越高时,其延展性越强,可维持较高的减薄率而不开裂。
图11 不同温度下最大主应变随应变速率的变化
分析结果与优化
为保证热成形后零件的使用性能,在CAE 分析阶段一般要保证减薄率不超过15%,且不能出现叠料现象。图12 为在加热温度950℃,转移时间8s,工具体初始温度75℃,摩擦系数0.45,压机下行速度参照压机动作曲线条件下获得的仿真分析结果。
图12 减薄率分布
图12 中监控的6 个点中,存在5 个点减薄值超出-15%,开裂风险极大;一处增厚。在初始参数下该区域处于可控状态;而在“参数对热成形过程的影响”小节所述的热压参数中,可通过工艺或模具处理变更的参数有摩擦系数,拉延筋几何尺寸和压边间隙。
⑴降低摩擦系数。
图13 为将摩擦系数降低至0.4 时获得的仿真结果,图中监控的6 个点中,5 个点减薄值相对初始参数有明显降低,同时端部增厚率为18%,观察成形过程,该区域在成形过程中存在叠料。
图13 降低摩擦系数后的减薄率分布
⑵调整压边间隙。
在叠料与开裂共同存在时,优先解决叠料缺陷。解决叠料的方式通常为通过增大板料,加高拉延筋,减少压边间隙以实现压边力的增加。而增加压边间隙对减薄率和成形过程的影响与降低摩擦系数类似,即降低了两侧的流料阻力,从上述降低摩擦系数的结果分析,该手段可以有效降低减薄率,但零件在成形过程中已出现叠料现象,该手段无法解决该零件成形过程中产生的开裂和叠料缺陷。
⑶产品局部优化。
通过以上调整参数后的分析对比,工艺参数改变并不能完全消除零件成形过程中存在的开裂和叠料风险。在消除叠料的情况下,零件存在开裂风险,均处在零件圆角区域。较直接的方案为更改局部产品造型,减低加强筋深度或增大圆角以降低减薄率,消除开裂。图14 为降低加强筋深度后的进行仿真的减薄分布图,通过该方案实现了踏板横梁的工艺开发并使得该零件成功量产,图15 为冲压产品实物。
图14 更改造型后的减薄分布图
图15 冲压产品实物
结论
⑴通过踏板横梁的热成形工艺开发,验证了22MnB5 在热冲压过程中的评价指标,掌握了各参数对热成形过程的影响,为同类型拉深成形工艺积累了宝贵的经验。
⑵通过踏板横梁的热成形工艺开发,扩宽了22MnB5 热成形零件的产品序列。
⑶通过增大局部圆角的方式可以有效降低热冲压后零件的减薄率,保证整体的强度和刚度,在开发前期需尽早识别。
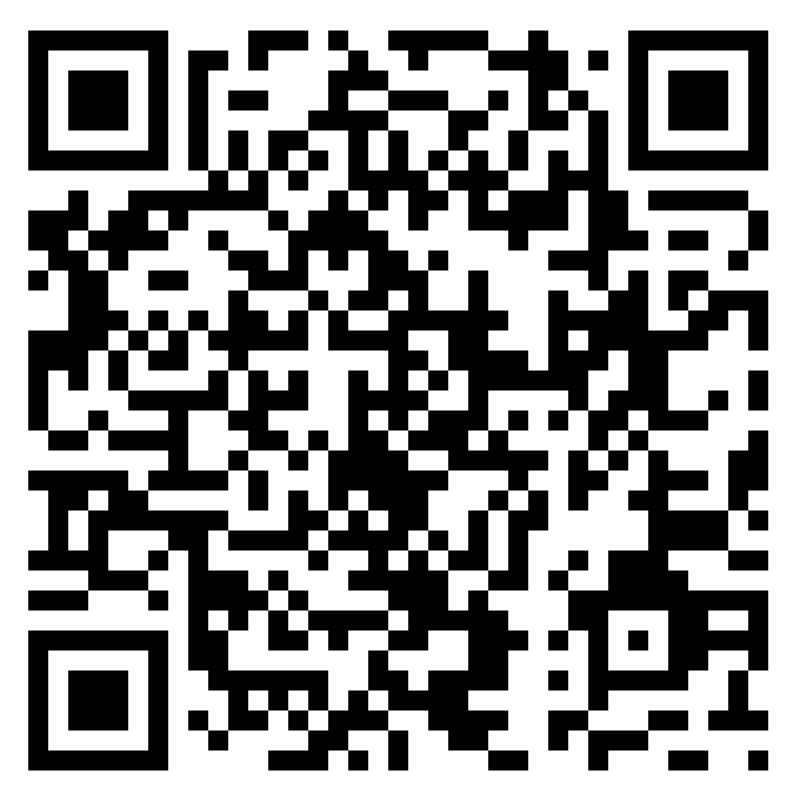